How to Select Rotary Encoders for Industrial Motor Applications
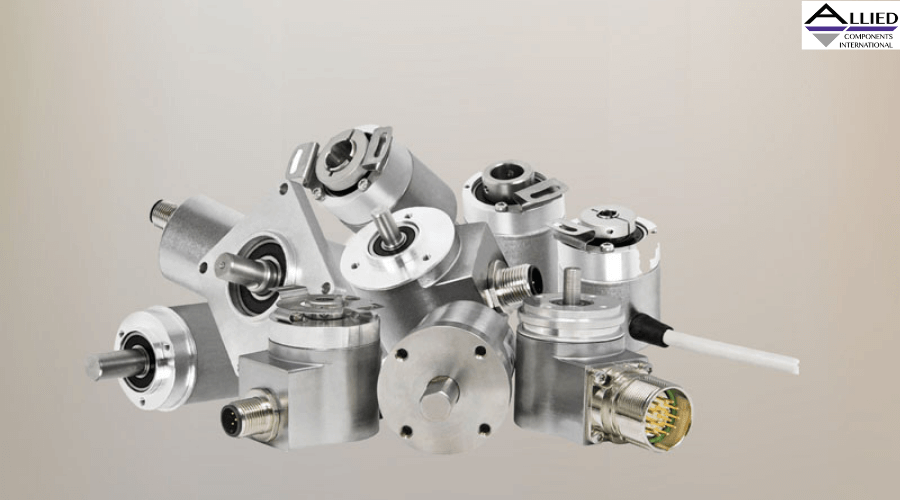
Applications of encoders in tracking the spinning of motor shafts in automated industrial systems and robotics continue to increase. These sensors detect and convey the rotor shaft’s digital position and motion data, helping maximize motor operational efficiency.
Here’s a brief guide on choosing the best rotor shaft tracking encoders for various industrial motor applications.
Choosing Between Absolute and Incremental Rotary Encoders
An incremental encoder tracks rotor shaft position relative to the reference point and is cheaper as well as more straightforward to implement. Conversely, an absolute type tracks each possible rotor position, making it easy to get an immediate response. It’s highly suited to safety-critical encoder applications.
The Best Encoder Type for Heavy Duty Industrial Applications
You may implement motor rotor shaft sensing in three main ways:
- Optical sensors - While these are common, they are ill-suited to heavy-duty industrial conditions where the presence of materials like grease or debris may compromise the accuracy of results. They’re prone to vibration or shock damage and often require time-consuming exact alignment.
- Magnetic encoders -These sensors don’t have any line-of-sight impairment, but they use a lot of power and don’t support high resolutions.
- Capacitive absolute encoders - Of the three sensor types, these encoders are the most suitable for heavy-duty environments. Their performance isn’t affected by debris and they’re immune to high temperatures and vibrations. They also last longer and generate far more precise data than their magnetic alternatives.
Encoder Integration Interfaces
Once you’ve selected the right type of encoder, you’ll need to develop the most efficient way to integrate it with the host system. Typical interfacing techniques include:
- Serial peripheral interface (SPI) - You can use this bi-directional interface to integrate an encoder in communication applications involving comparatively short interconnect distances.
- RS-485 - This interface is ideal for industrial environments with significant levels of electrical noise or electromagnetic interference (EMI). Unlike SPI, this application of encoder interfaces doesn’t require data rate reduction in situations involving longer interconnect distances. You can even achieve data speeds of up to 10 Mbps if you use a dedicated RS-485 receiver. You can also connect multiple encoders to one bus with this type of interface.
- Synchronous serial interface (SSI) -This is a highly cost-effective interface for applications of encoders in monitoring rotor shaft position and speed. In this simplex, one-way communication system, a common clock signal guides both the receiver and transmitter in synchronizing the information sent via SSI. It supports the same interconnect distances as SPI. Like the SPI interface, SSI offers superior noise tolerances.
Capacitive absolute encoders are highly reliable electromechanical devices for many heavy-duty rotary shaft tracking applications. Visit our Allied Components International website to learn more about our comprehensive catalog of cutting-edge magnetic component products.